Why NASA turns to AI to design mission hardware?
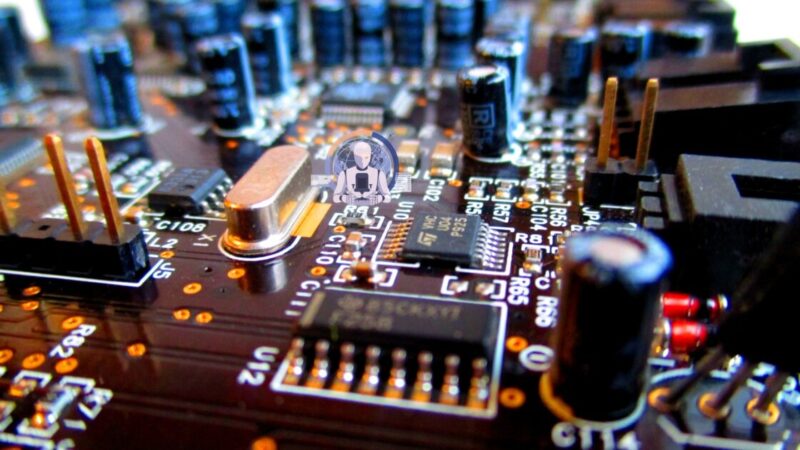
Turning to Artificial Intelligence (AI) to design mission hardware is becoming increasingly popular among NASA projects as AI-designed parts are lighter, more structurally sound, and can be designed much quicker than with traditional methods.
Ryan McClelland, a research engineer at NASA’s Goddard Space Flight Center, Greenbelt, Maryland, has pioneered the use of off-the-shelf AI software for evolved design. This process begins with the mission’s specific requirements, which are then used to define the surfaces where the part must connect to other hardware, as well as any bolts and fittings. The designer, according to NASA, must block out a path to prevent the algorithm from blocking optical sensors or laser beams. Once this is done, the AI connects the dots to produce a complex structure design within a few hours.
McClelland noted that that process “needs a human eye” to ensure that the structure isn’t too thin. However, parts designed with AI can save up to two-thirds of the weight compared to traditionally designed components, and can be fabricated in as little as one week. Furthermore, the stress analyses of these parts reveal that they are almost ten times lower than those designed by a human designer.
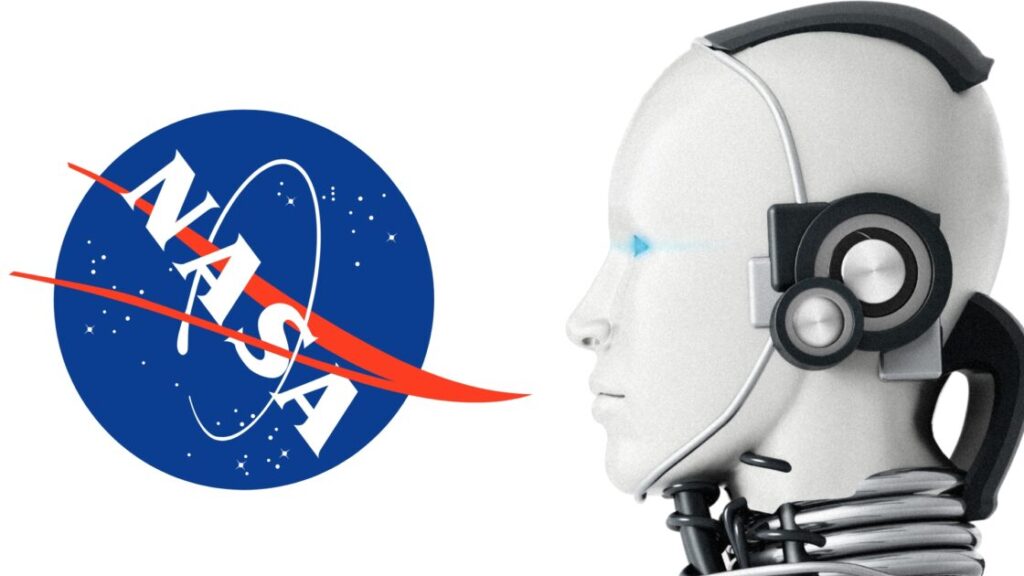
NASA missions in various stages of design and construction have adopted the use of these AI-designed parts, from Earth-atmosphere scanners and space weather monitors to the Mars Sample Return mission.
The EXoplanet Climate Infrared TElescope (EXCITE) mission is a particularly good example of AI’s capabilities. This balloon-borne telescope is designed to study exoplanets orbiting other stars and was having difficulty meeting its design requirements. However, McClelland designed a titanium scaffold for the back of the telescope which connected an aluminum cryogenic chamber to a carbon fiber plate, allowing for the different thermal expansion properties of these materials without stressing either one.
AI-assisted design is becoming an invaluable tool in the industry, as the need for custom parts is far greater than for mass-produced items. With the addition of 3D printing and in-situ resource utilization, the future of In-space Servicing, Assembly, and Manufacturing (ISAM) is looking brighter. This is a key priority for U.S. space infrastructure development, as outlined in the White House Office of Science and Technology Policy’s ISAM National Strategy and Implementation Plan.
Auto Amazon Links: No products found.